Why Therelek ?
Over 45 years of established expertise. Over 5500 heat treatment furnaces, integrated heat treatment systems and solutions delivered so far, worldwide. A distinguished Commercial Heat Treater, with the most stringent quality certifications, an exhaustive process capability range and customer approvals from some of the world’s most quality conscious organizations.
By managing and maintaining a state of art heat treatment facility with processes ranging from Hardening to Nitriding, Solutionizing to Vacuum Annealing & Brazing, we as users ourselves build furnaces and integrated heat treatment systems that are built-to-last in construction, easy to maintain and are result-oriented in performance.
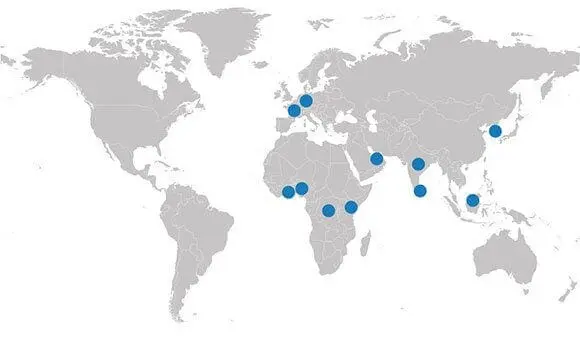
As a heat treatment furnace OEM cum end-user (heat treat service provider), our knowledge base is constantly expanding, and we use the same knowledge to continuously improve our products, services and costs.
THERMAL EXCELLENCE ENGINEERED
Bogie Hearth Furnace
Our standard bogie hearth furnaces range is available up to 1500°C, however, we make custom designed furnaces for any special requirements. High temperature applications are hardening, normalizing, sintering whereas low temperature applications are post weld heat treatment (PWHT), stress relieving, tempering & annealing.
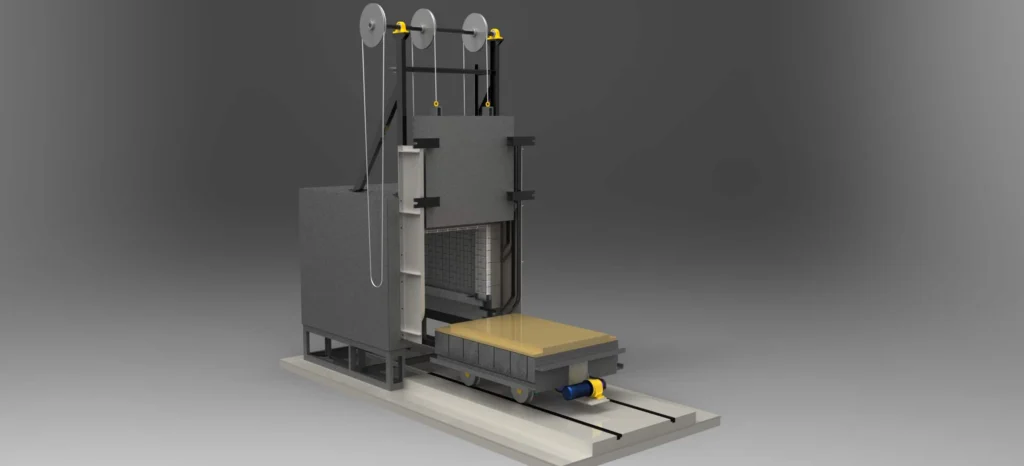
Chamber Furnace
Therelek’s chamber furnaces are available with operating ranges up to 1850°C. These furnaces are usually rugged, refractory based construction or lightweight ceramic fiberboard and insulation based in construction to ensure optimal thermal performance and efficiency.
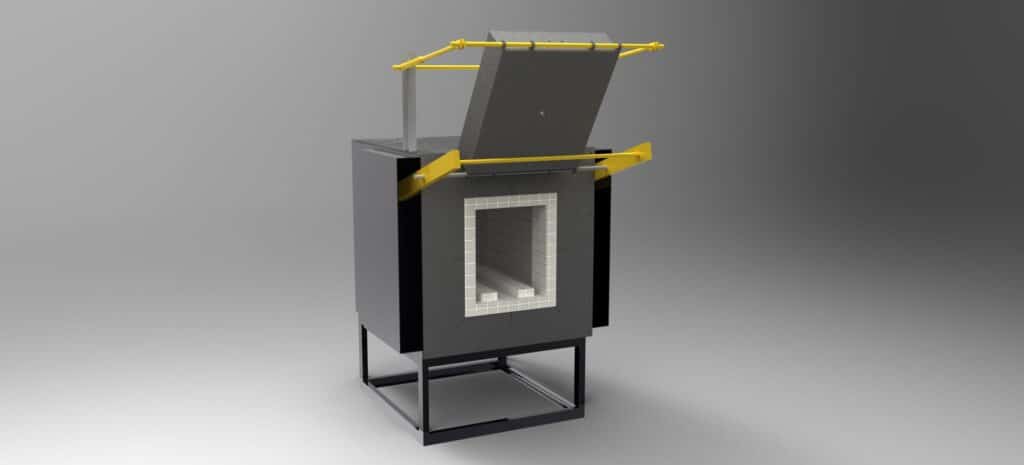
Chamber Oven
Chamber ovens or low temperature air circulation ovens have a wide area of application from baking ovens curing ovens to ageing ovens. The ovens can be designed with complete inner stainless steel construction for long life.
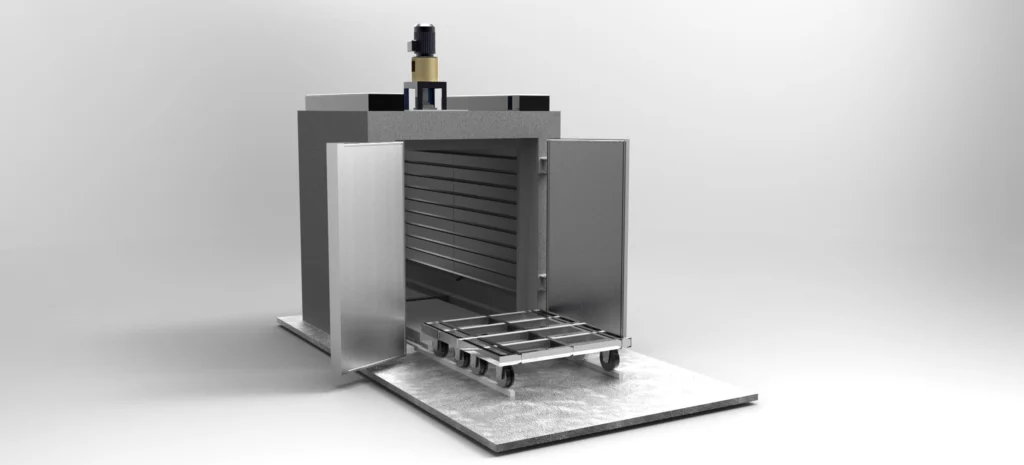
Continuous Mesh Belt Oven
Continuous Mesh Belt Oven is usually multi zone controlled for better process control. Individual zones can have preset temperature controls for best process results.
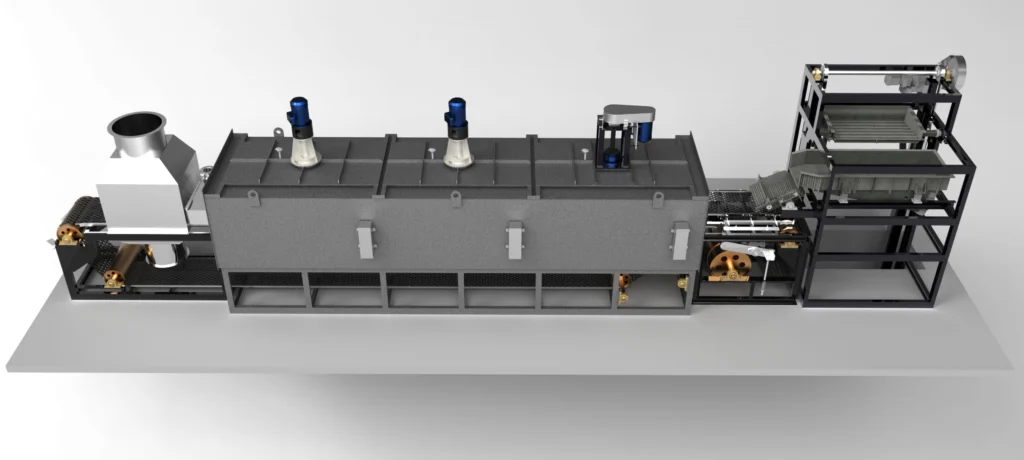
Continuous Mesh Belt Furnace
A multi-zone control environment is present in a continuous high temperature furnace, often with a single pre heating zone, followed by multiple heating zones and then cooling zones before exit.
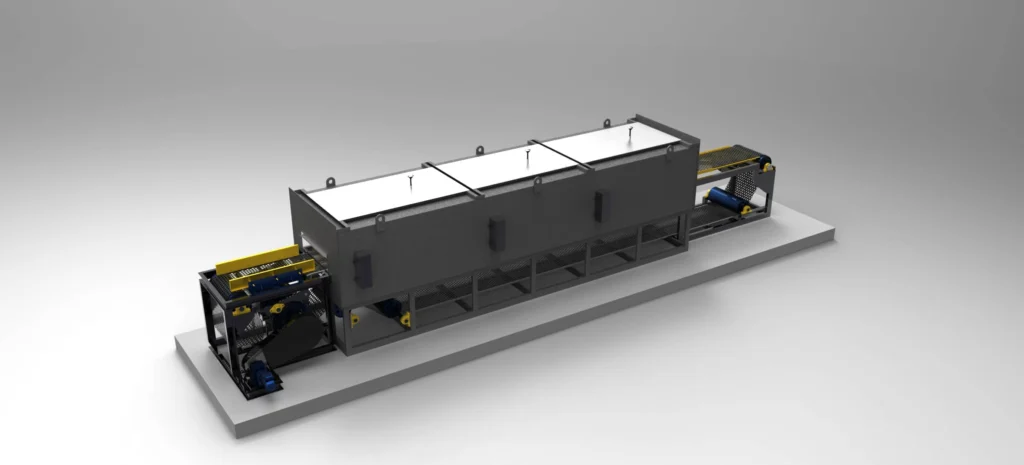
Continuous Pusher Furnace
Therelek’s pusher type continuous furnaces can be designed up to operating temperature range of 1800°C.These furnaces can be customized to requirements that need process specifications design with various operating atmospheres including hydrogen and nitrogen.
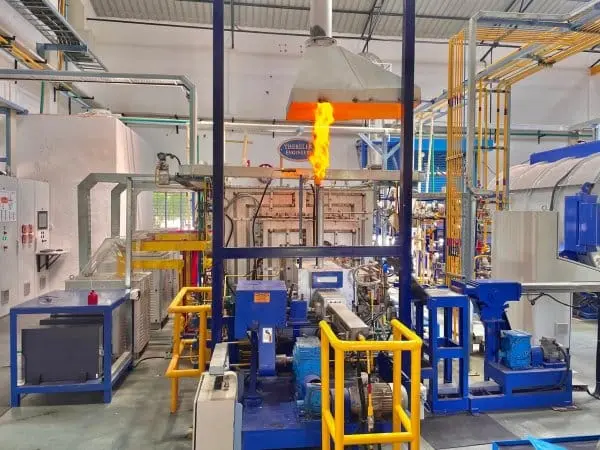
Continuous Roller Hearth Furnace
Roller hearth furnaces are designed for continuous production and Easy handling and transfer of large sizes and weights to handle large size and weights. contnious roller hearth furnaces are used forging parts, bearing and various semi finished parts.
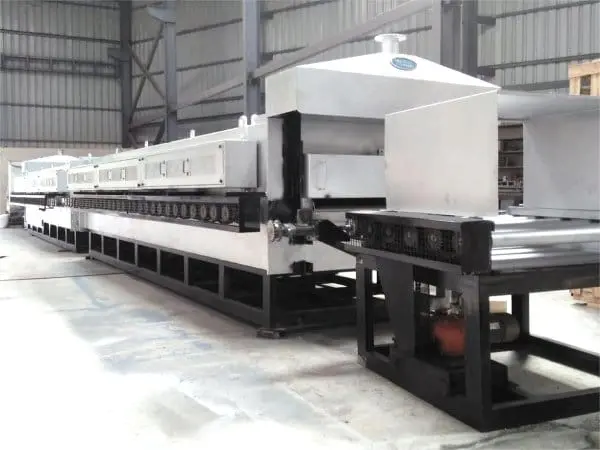
Drop Bottom Quench Furnace
The Drop Bottom Furnace is the inverted type with charge lifting and lowering facility to accommodate the high speed quenching including de clamping, door opening and quenching. These are used for aluminium structures, aluminium casting, aerospace alloys, and can be designed as per latest AMS specifications.
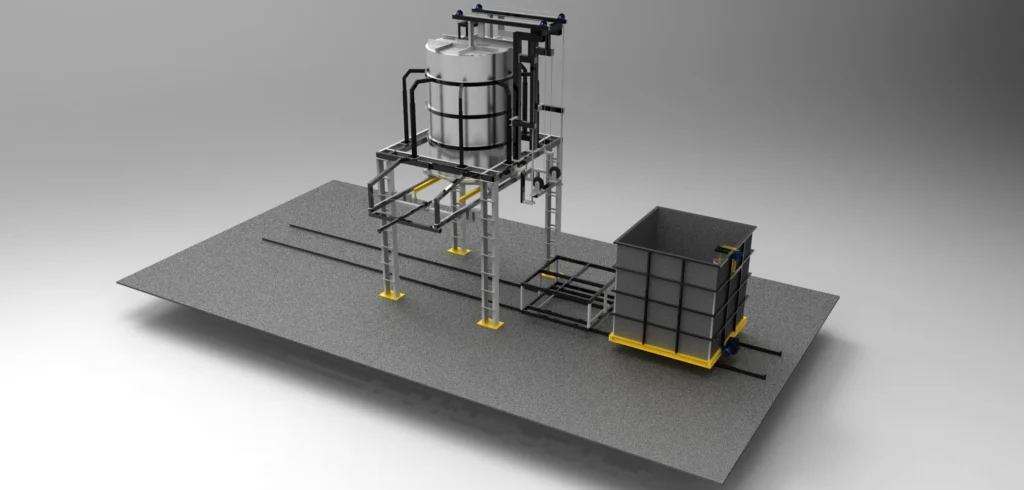
Pit Furnace
Our pit furnaces are designed and manufactured for very small to very large workpieces. Pit furnace is available with or without retorts in customized dimensions and variations to carry out the complete heat treatment process.
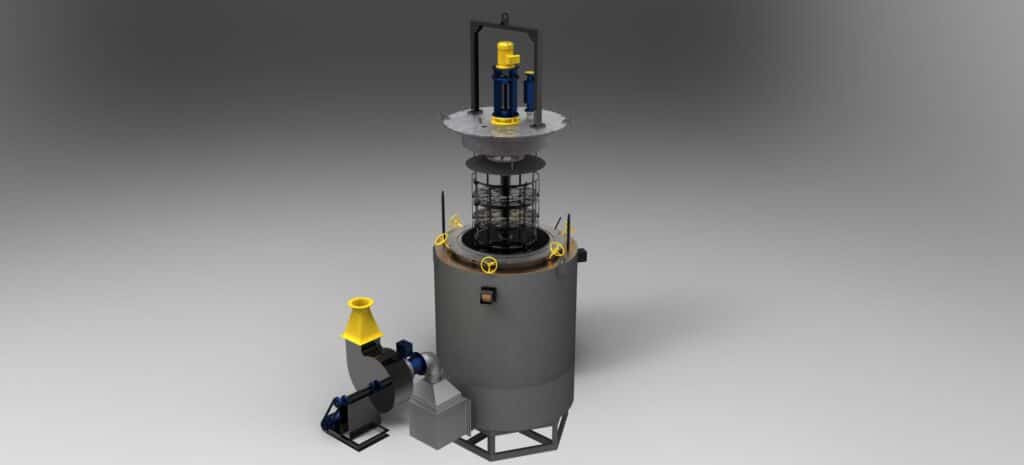
Sealed Quench Furnace (SQF)
The sealed quench line consists of dual chamber sealed quench hardening, carburizing, preheating and tempering furnaces, washing machines, stationary table, hydraulic lifts and charge transfer systems.
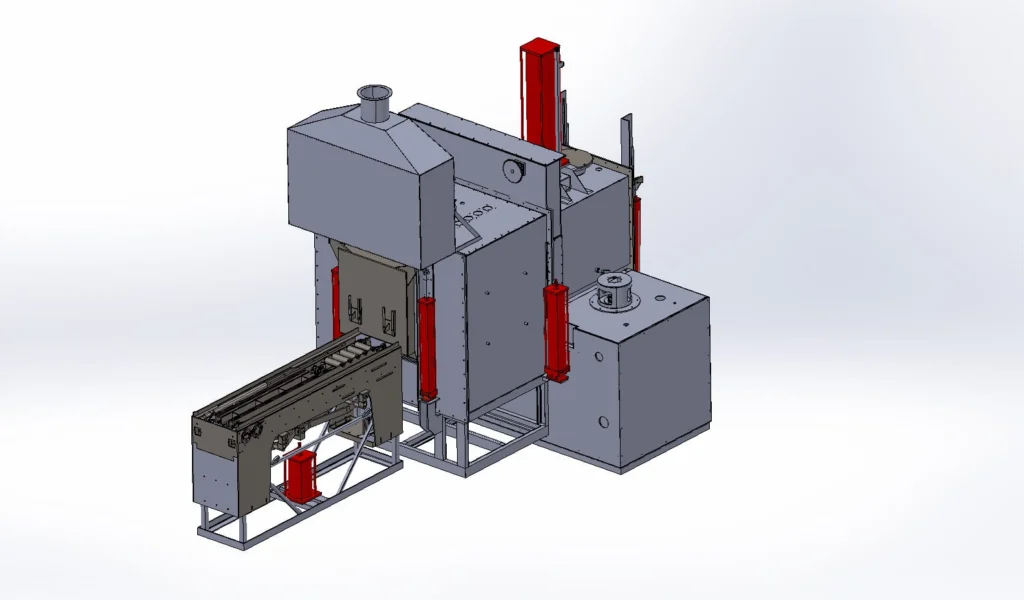
Raising Hearth Furnace
Raising hearth furnaces are available up to very high temperature configuration with operating temperature till 1850°C, with silicon carbide
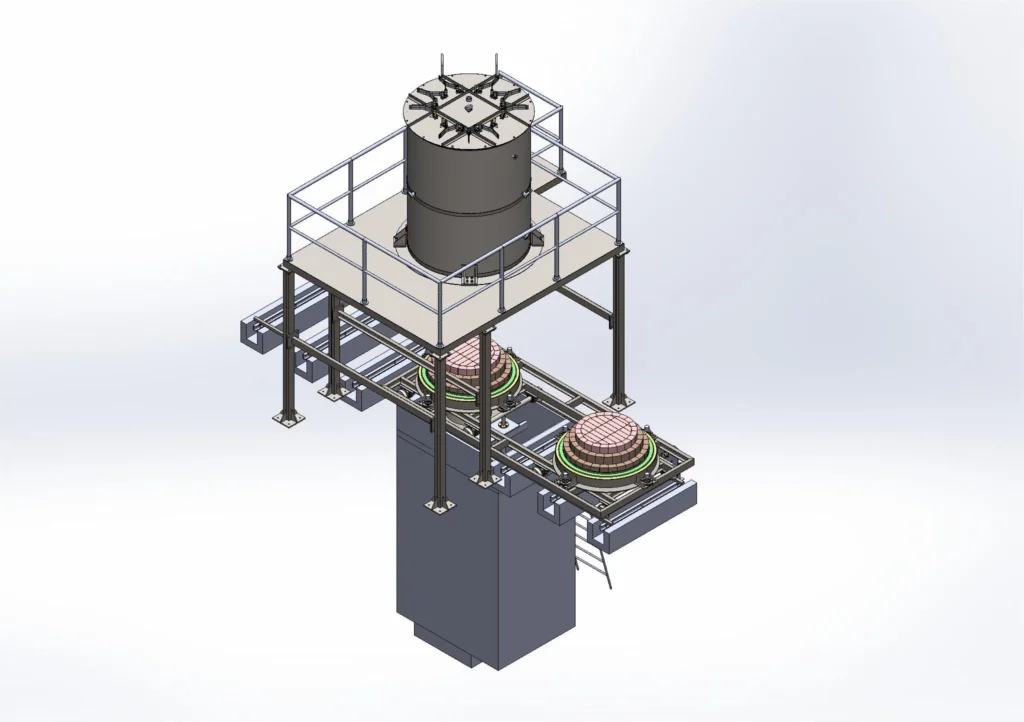
Rotary Calciner
Multi-zone control electrically heated rotary calciners of varying lengths depending upon output and function are selected for even, uniform and controlled heating across the length of the rotating drum / rotating tube.
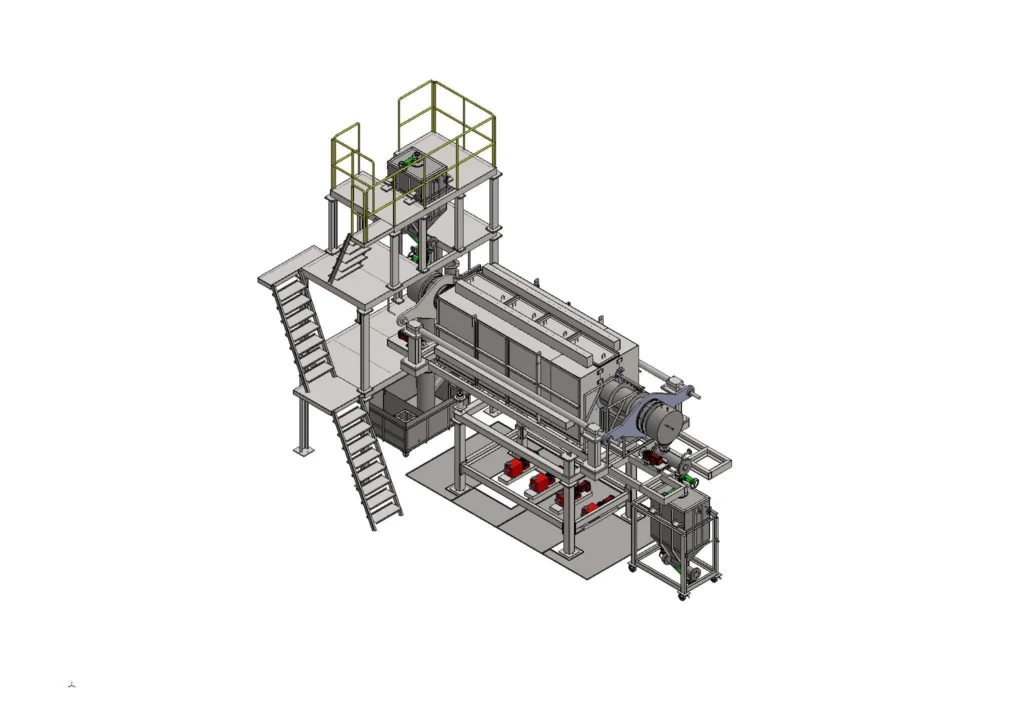
Rotary Kilns
The material is processed in the rotating drum at high temperature for a precise time to induce a physical change and is kept inclined to assist the moving material inside.
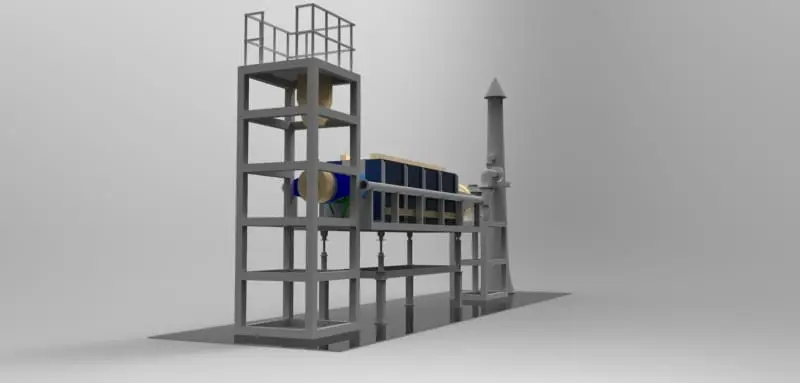
Plasma Nitriding Furnaces / Ion Nitriding Furnaces
Therelek manufactures plasma nitriding furnaces / ion nitriding furnaces of hot wall or cold wall type with bell type construction.The bell works motorized lifting movement….
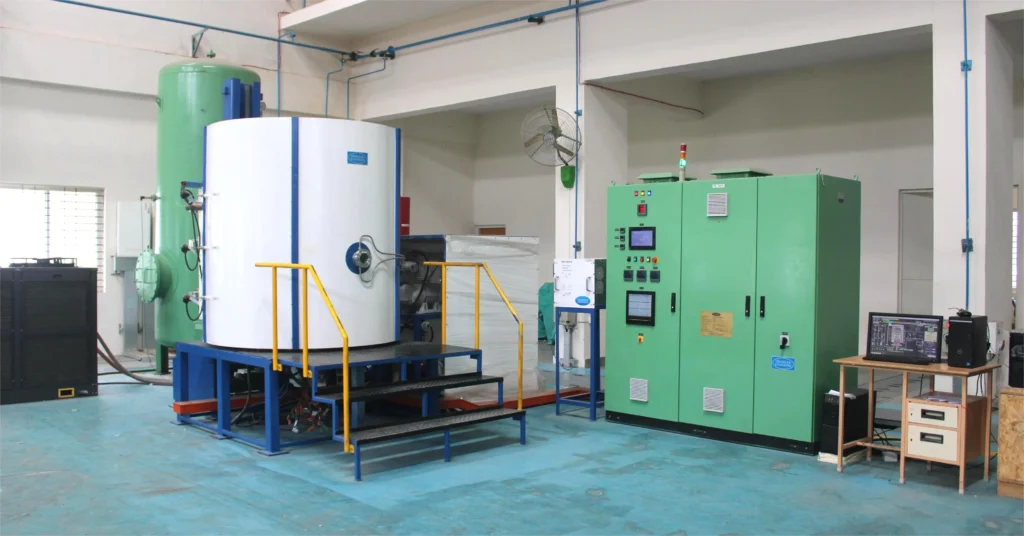
Vacuum Furnace
Vacuum heat treatment or thermal processing of components at low pressure or vacuum has been the choice of niche and high technology industries like aerospace, space research and Special process, and for various heat treatment application like hardening, tempering, annealing, brazing & sintering.
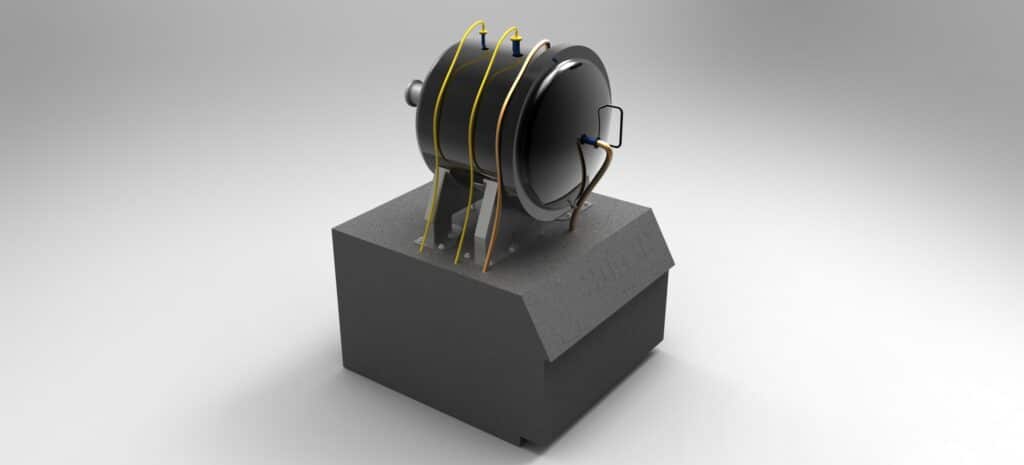
Horizontal Vacuum Furnace
Therelek’s Horizontal Vacuum Furnace is known to have a sturdy cold wall as a structure with a metallic or graphite hot zone
Vertical Vacuum Furnace
Power consumption is found to be comparatively lower in case of the vacuum furnace, than that of the salt bath furnace
Vaccum Carburizing furnace
Therelek Engineers manufactures vacuum carburizing furnaces or systems for various industries across different sectors, apart from other heat treating and co related applications. Our vacuum carburizing furnaces cater to numerous industries like automotive, defence and aerospace.
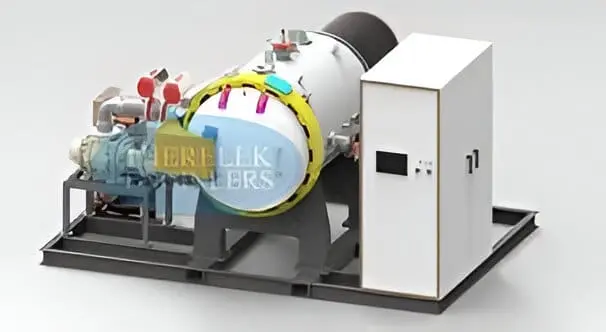
Vacuum Induction Melting Furnace
Vacuum Induction Melting furnace (VIM) is used in secondary refining or in metallurgy, to refine alloys in a fluid state, by bringing some change in temperature and their chemical compositions.
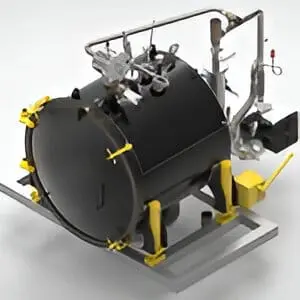
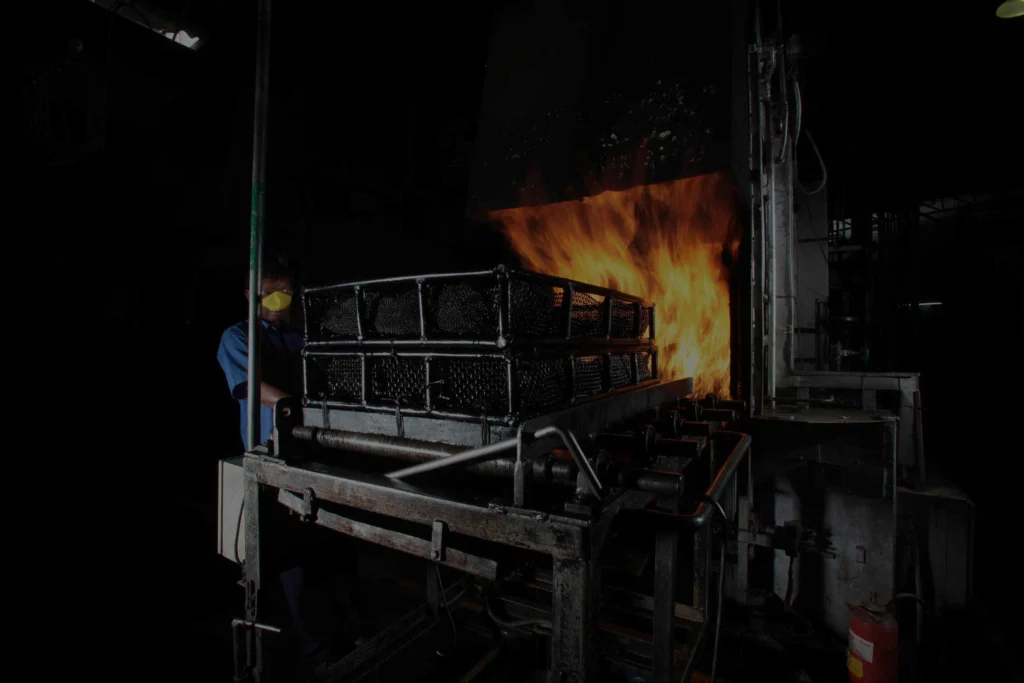
Discover our
heat treatment services
The key to world class commercial heat treatment is process control. Process control makes it possible to attain desired result repeatedly with minimum deviation. This is where Therelek excels – continuous standardization and refinement of processes, process documentation and traceability, meticulous planning and scheduling – all of which assure timely, cost-effective results to delight our customers.
Our products and solutions are not only comprehensive, but complete
As a heat treatment furnace OEM cum end-user (heat treat service provider), our knowledge base is constantly expanding, and we use the same knowledge to continuously improve our products, services and costs.
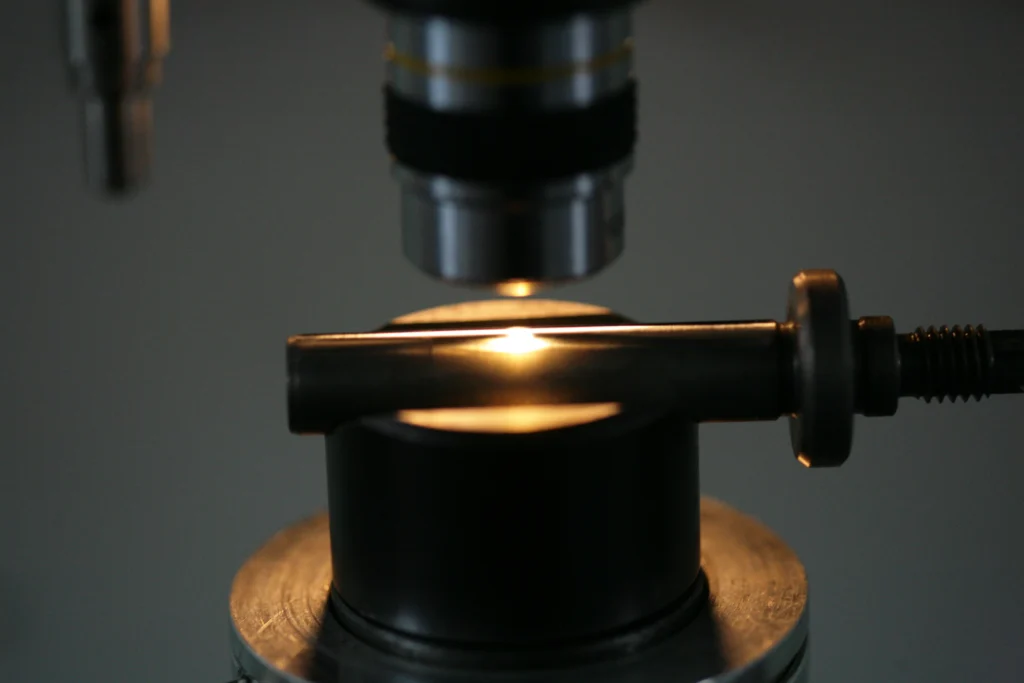
Quality from Start to Finish
Only the best material and manufacturing processes go into the makings of our products and services
NADCAP Certificate
AS 9100:2016
ISO 9001:2015
NABL ISO/IEC 17025:2017
ISO 14001:2015
ISO 45001: 2018 HEALTH AND SAFETY MANAGEMENT SYSTEM
From Industry Leaders to Global Multi-National organization
Approvals from our
Reputed Customers
- Airbus
- GE Aviation
- BELL Helicopter
- Pratt & Whitney
- Avio ‐Italy
- Collins Aerospace Systems
- CESA
- HAL-Hindustan Aeronautics Limited
- Schaeffler
- Volvo
- Boeing
- Rolls Royce
- Safran
- Rafael
- Liebherr Aerospace
- Moog
- Parker
- Snecma
- Tata group
- Bosch Rexroth
- Lockheed Martin
- Bombardier
- Thales
- Hamilton Sundstrand ( UTC Aerospace systems )
- Caterpillar
- Ford
- Larsen & Toubro Limited
- Messier Bugatti Dowty
Trusted by over 2,000 satisfied customers worldwide
Blogs
Frequently Asked Questions
Bogie Hearth Furnace is a special type of chamber furnace. The housing of the furnace can be accessed from one side through a manually or electrically operated moving trolley coupled to a door system.
The trolley or bogie can be designed with virtually any product-specific supports or component tracks. In addition, the loading capacity is almost unlimited.
A Batch or a chamber furnace is used in numerous production and laboratory applications for thermal processing. The heat treatment is essentially executed in batch process, where the material is loaded to a basket or directly in the furnace and then heat treated. Unlike continuous furnace, the material with lesser to medium volume and custom size equipment are loaded in Chamber Furnaces.
Continuous air circulation conveyor furnace or ovens are offered for constant, high production jobs.
Our furnaces are used for Stress relieving, Tempering and similar low temperature processes that needs air circulation.
They are also used for drying parts after processing & painting and also in filter manufacturing industries for pleating, setting and curing of filter papers.
Continuous furnaces are classified according to the number of heating zones, the method of moving the heated parts continuously through pre heating, soaking & cooling zones.
The temperature in continuous furnaces is constant over time and variable over the length of the furnace. In the heating and soaking zones the temperature is almost constant; in the holding zone it decreases toward the front of the furnace.
Digital Manufacturing Resources
Join 2,400+ companies who choose Fabrik for fast, high-quality custom parts
- Instant pricing & lead-time options
- CNC Machining, Urethane Casting, Injection Molding
- Support from technical manufacturing experts